課題、悩みが一気に解消
渡邊製作所では、多くのお客様から組立作業を請け負っています。
組立作業について、様々な課題、悩みがありましたが、デジプロマスタを採用することにより、一気に解消しました。
そんな渡邊製作所の事例をご紹介します。
デジプロマスタの特徴
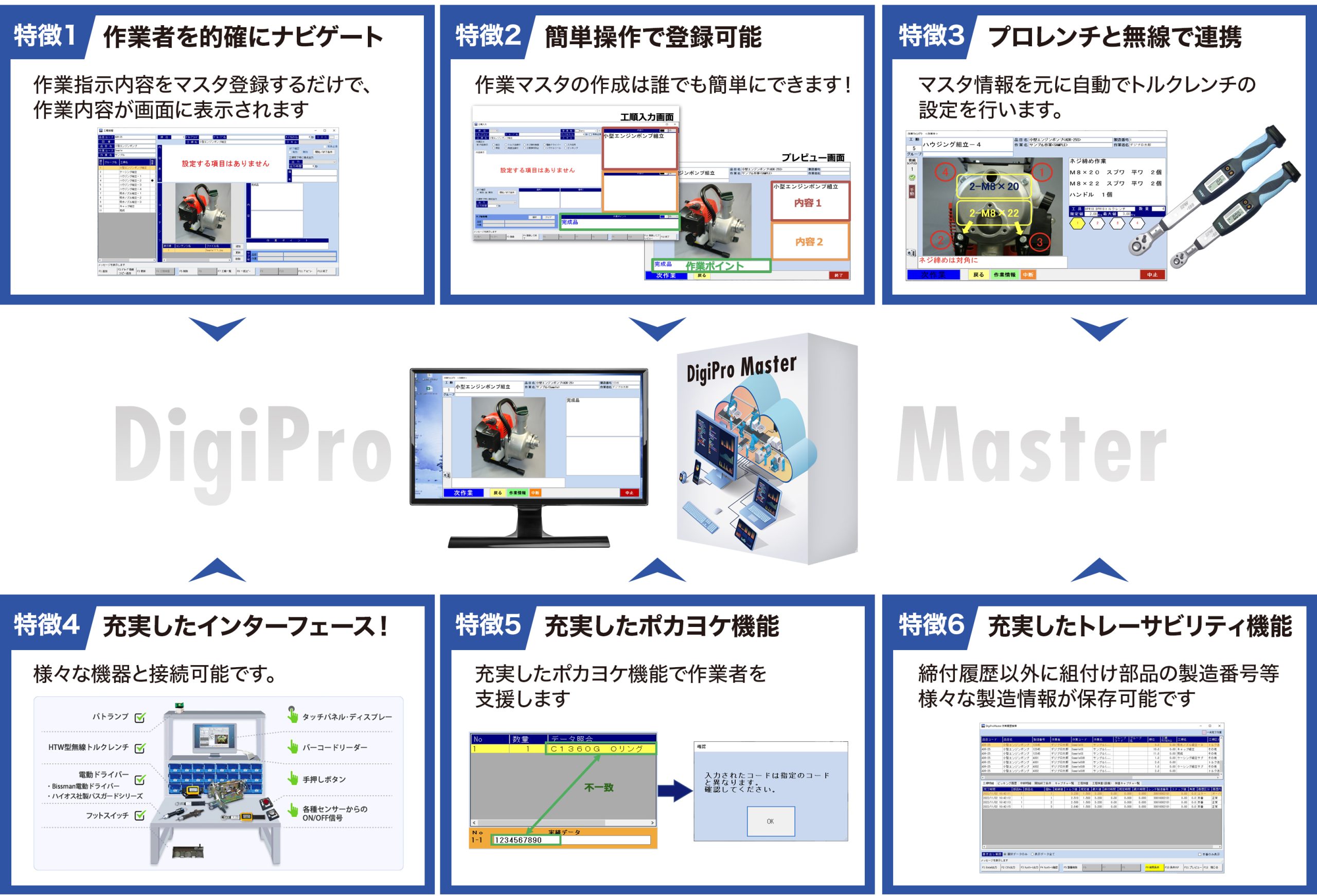
導入の経緯
渡邊製作所の組立グループは製品の機種ごとに作業者が決められており、技能継承は進めているものの、多能工化があまり進んでいない状況でした。
そのため特定の機種の受注が増えたときは、決められた作業者で対応するしかなく、作業者間で残業時間が偏ってしまうなど、仕事の負荷を平準化できていない状況でした。
また、機種により受注頻度は様々で、中には数年に1度しか受注が無い機種までありました。そういった製品は技能継承を進めるのが難しく、かと言って初めて組み立てる作業者が作業標準書を見ただけで組み立てられるわけでもなく、作業実績のある作業者が組み立てるしかありませんでした。
以下、当時の課題や悩みを表にまとめました。
課題、悩み
課題・悩み | 詳細 |
多能工 |
製品の機種ごとで作業者が固定されており、多能工化が進んでいなかった。そのため、作業者間で仕事の負荷が偏り、負荷の多い作業者は技能継承に時間を割けないといった悪循環が続いていた。 |
トルク管理の精度 |
アナログのトルクレンチでトルク管理を行っていたが、数値管理できていなかったので、きちんと数値で管理をしたい。 |
締め忘れの流出 |
ボルトを締め忘れることがあり、クレームが発生することがあった。 締め忘れを何とかしたい。 |
コスト削減 | トルクレンチの本数がどんどん増えていき、更新費用等のコストを削減したい。 |
工数削減 | 組立ながら、もしくは組立完了後にチェックシートを記入しているが、手間がかかる。 |
セルステーションの特徴と構成
セルステーション①組立(大)の場合
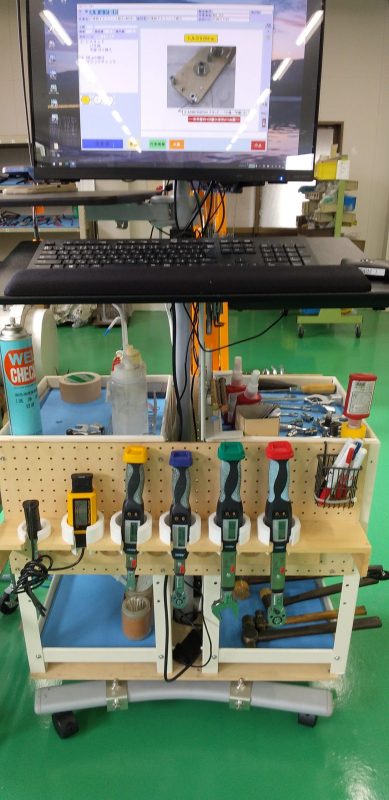
全体像
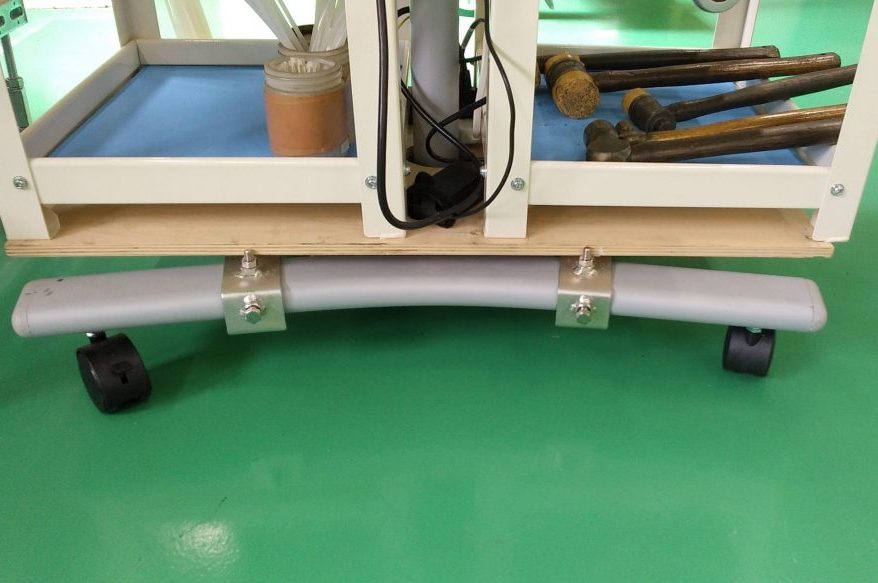
固定の作業台で組み立てられないものが対象なので、キャスター付きし、移動可能にしました。
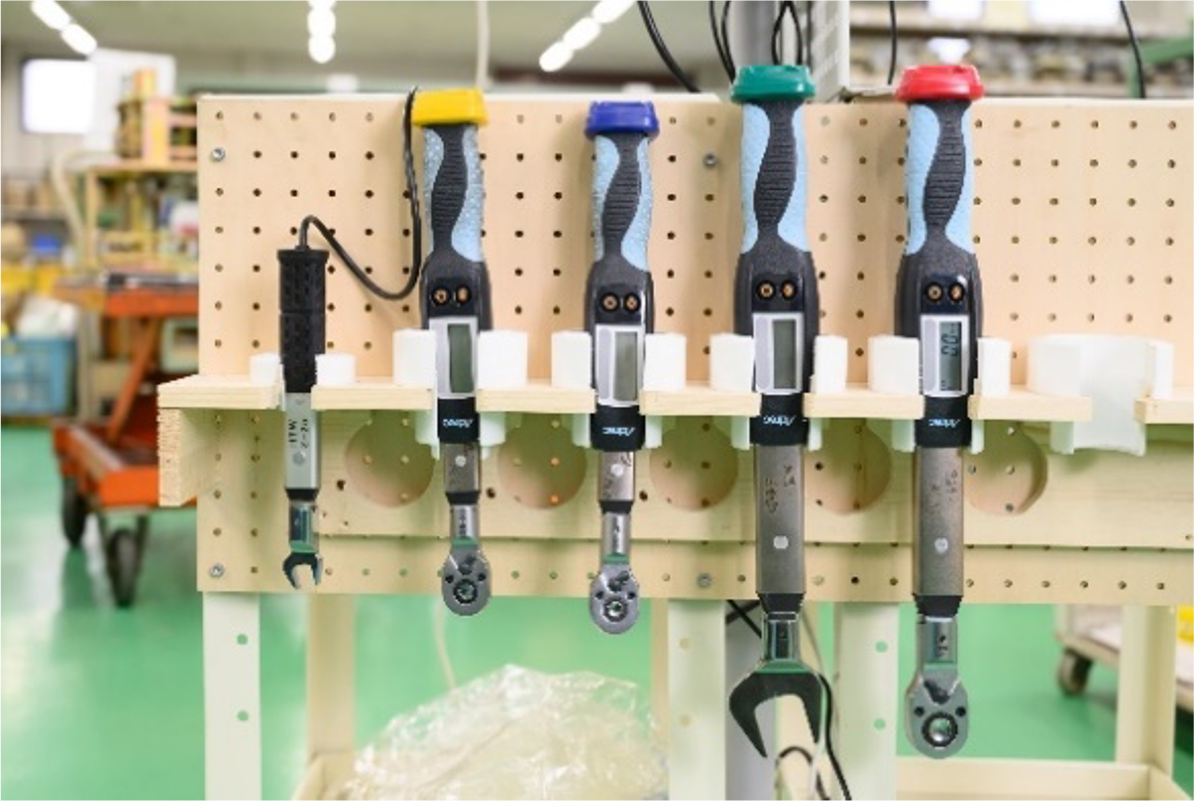
トルクレンチは全部で5本
ホルダーは既製品のモニタースタンドを改造しました。
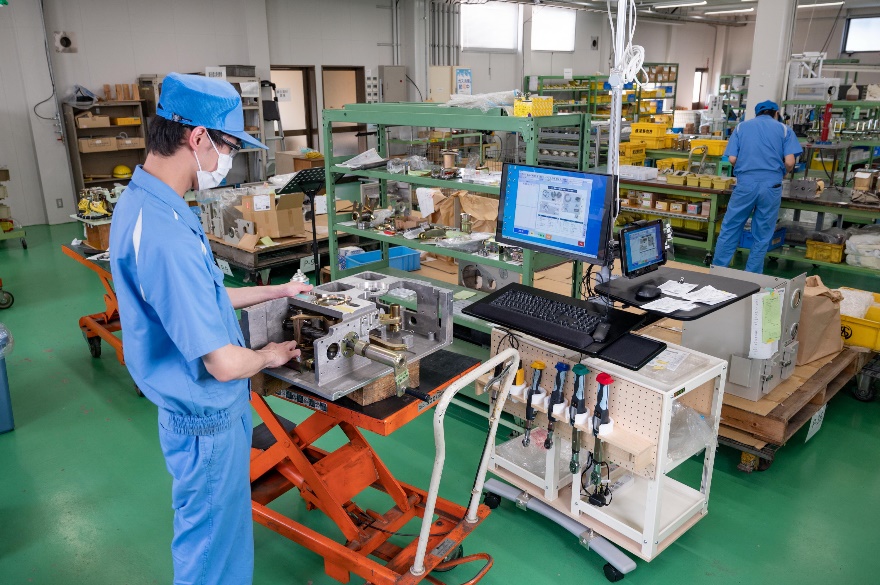
作業風景
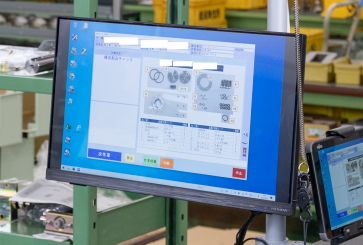
パソコンはタブレットを使用していますが、見やすいように大型の液晶画面に表示しています。
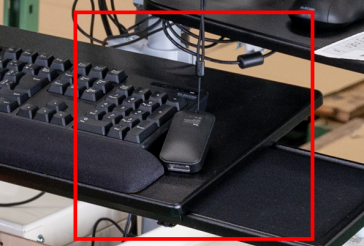
QRコードで作業指示Noを読み取り、作業を開始します。
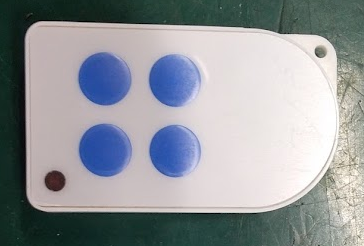
液晶画面はタッチパネルですが、モニターから離れている場合、リモコンで操作可能です。
セルステーション①構成図
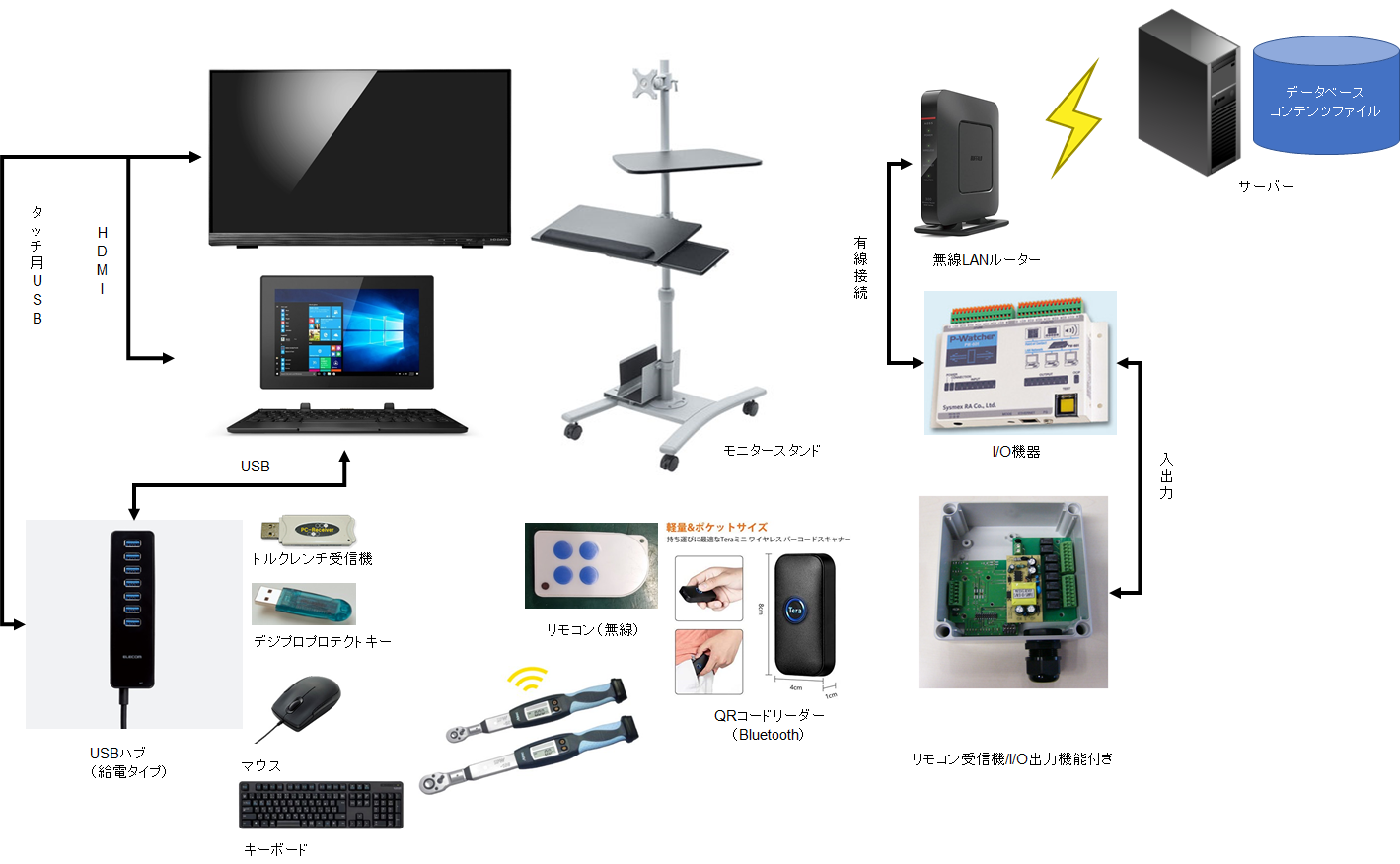
品名 | 型式 | メーカー |
モニタースタンド | CR-LAST3 | SANWA |
液晶モニター | LCD-MF224FDB-T | アイ・オー・データ機器 |
タブレット | Tablet 10 | Lenovo |
USBハブ | U3H-T719SBK | ELECOM |
トルクレンチ受信機 | ZC-202W | アドレック販売品 |
デジプロプロテクトキー | - | アドレック販売品 |
マウス | - | - |
キーボード | - | - |
QRコードリーダー | 1200-CCD | Tera |
I/O機器 | PW-601 | アドレック販売品(販売終了) |
無線・I/O変換機 | TSxx-4sw/8swRX-RL-NWP | 野村エンジニアリング |
リモコン | TS03 | 野村エンジニアリング |
セルステーション②組立(小)の場合
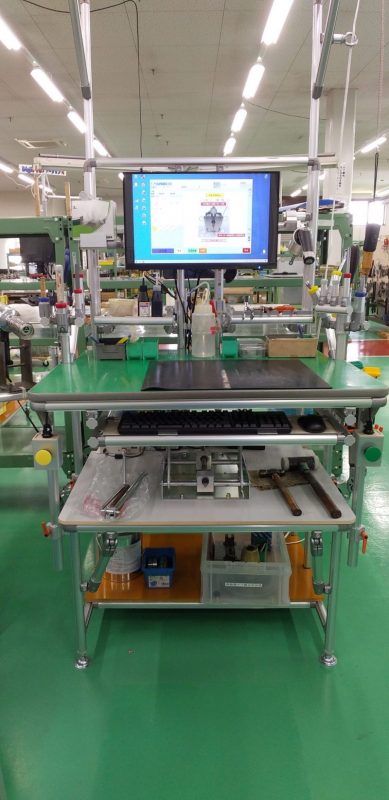
全体像
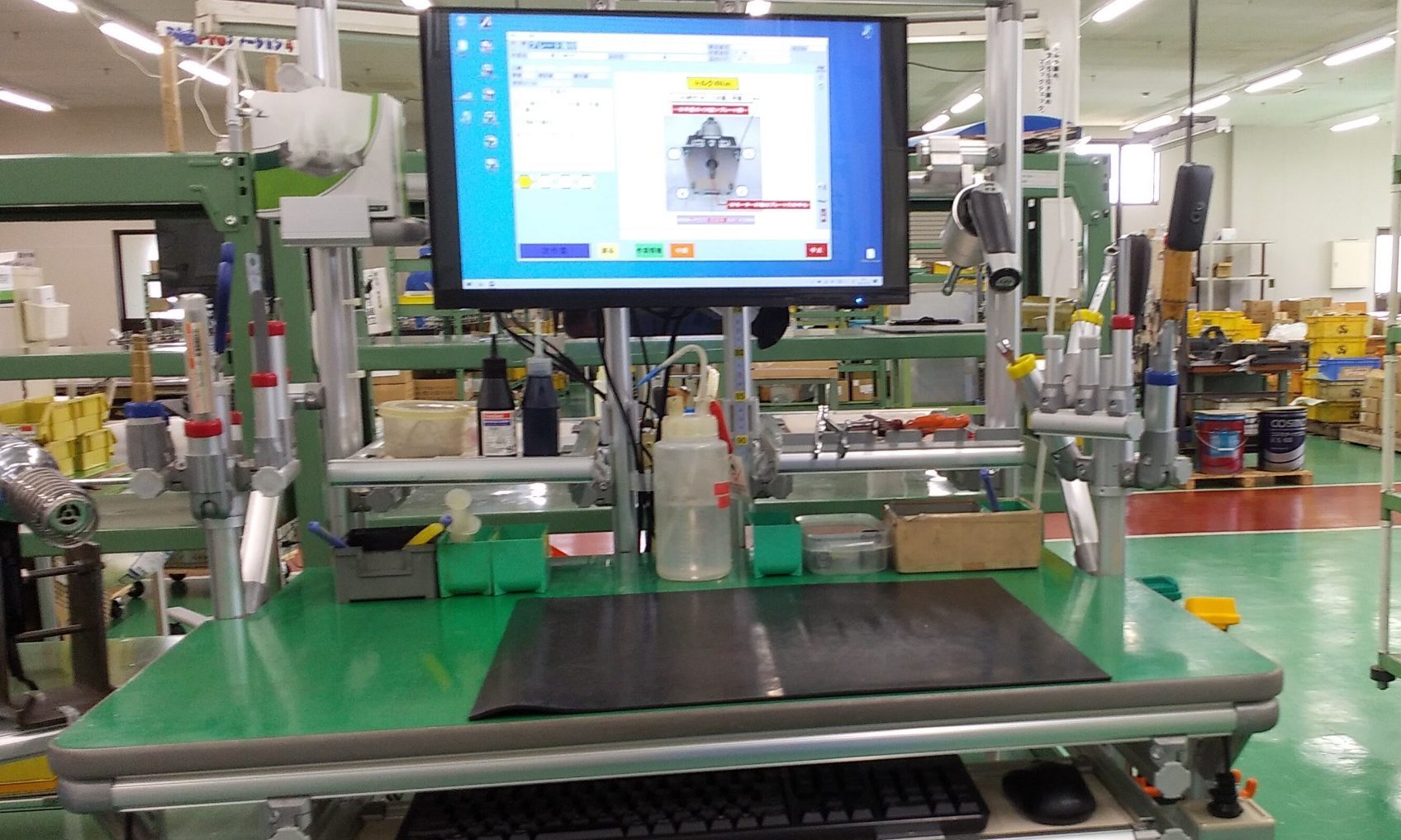
固定の作業台の上で作業します。主に小さいものが対象です。
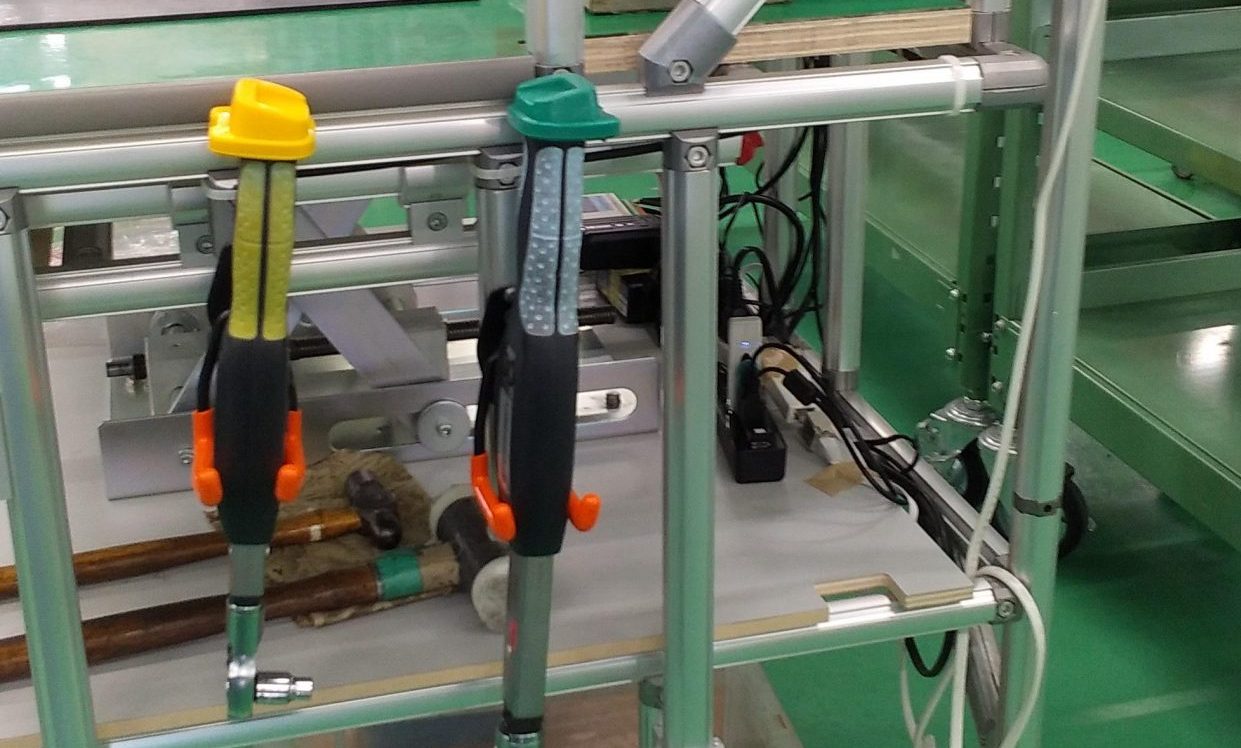
トルクレンチは全部で2本
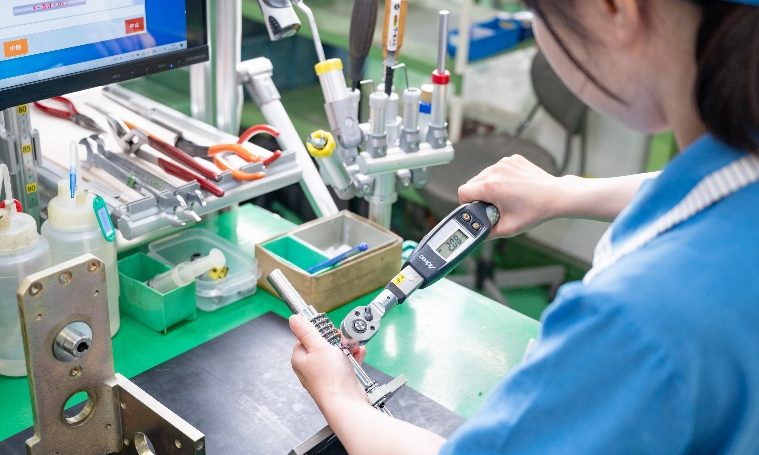
作業風景
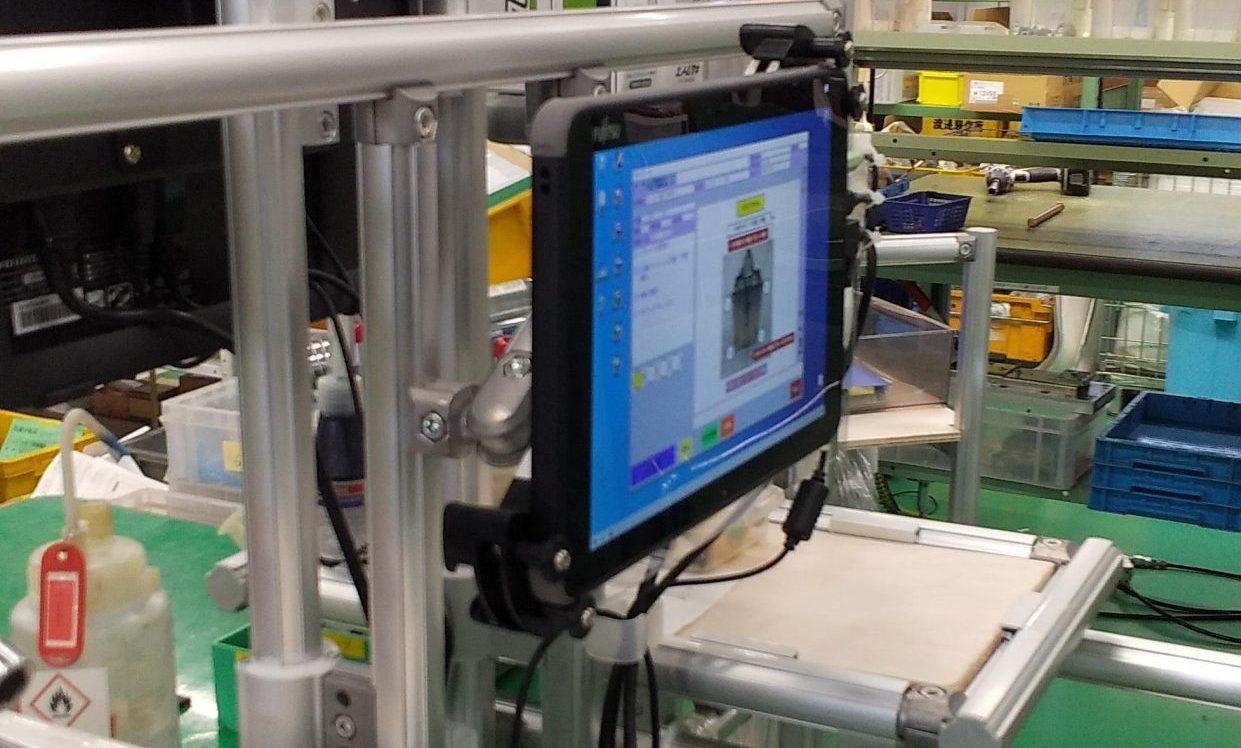
パソコンはタブレットを使用していますが、見やすいように、大型の液晶画面に表示しています。

使用する工具を取りやすいように配置しています。
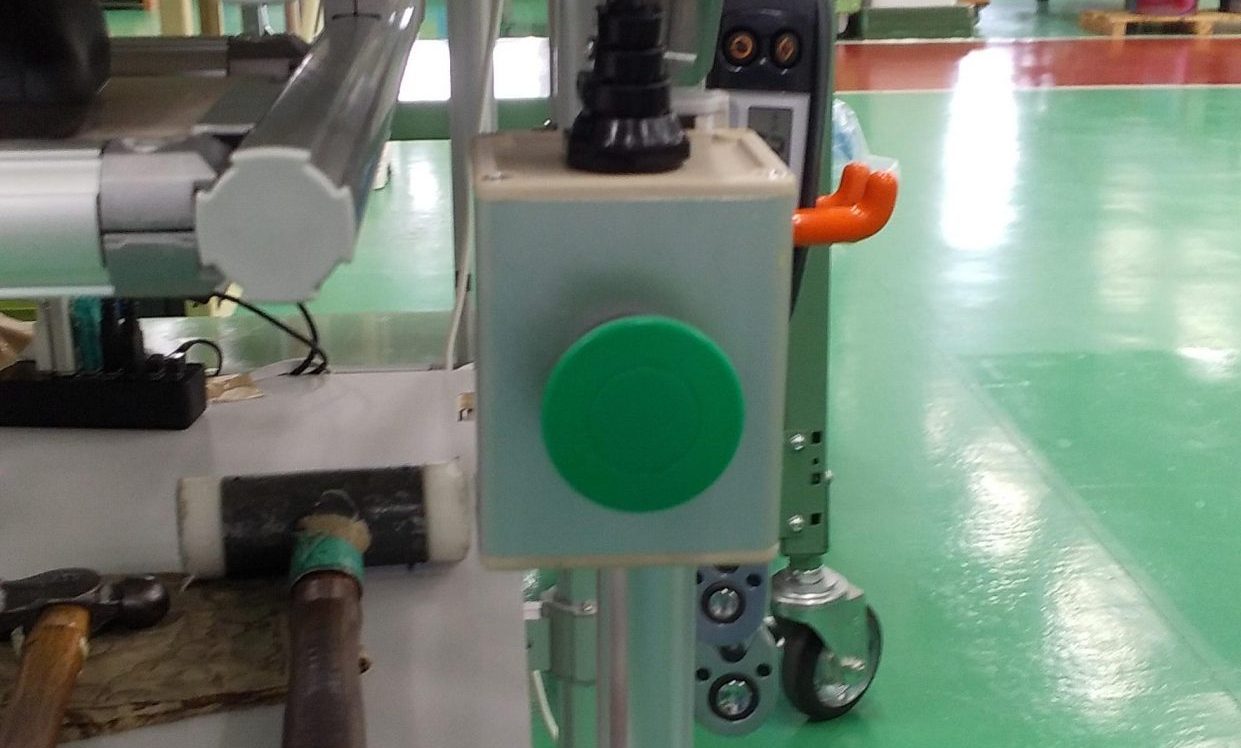
机の両サイドに押しボタンを設置し、画面送りの操作が可能です
セルステーション②構成図
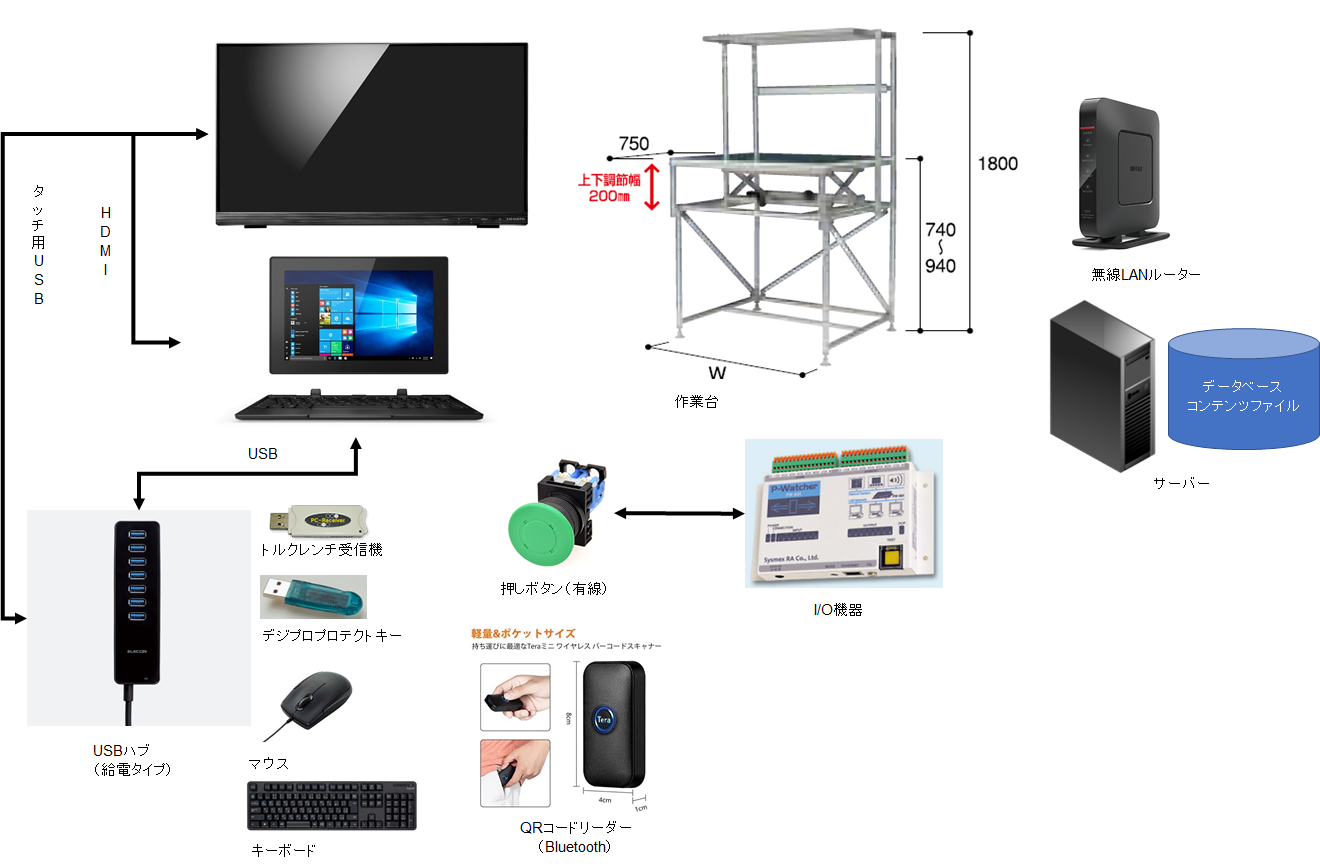
品名 | 型式 | メーカー |
作業台 | CR-LAST3 | SUS株式会社 |
液晶モニター | LCD-MF224FDB-T | アイ・オー・データ機器 |
タブレット | Tablet 10 | Lenovo |
USBハブ | U3H-T719SBK | ELECOM |
トルクレンチ受信機 | ZC-202W | アドレック販売品 |
デジプロプロテクトキー | - | アドレック販売品 |
マウス | - | - |
キーボード | - | - |
QRコードリーダー | 1200-CCD | Tera |
I/O機器 | PW-601 | アドレック販売品(販売終了) |
結果
課題・悩み | 結果 |
多能工化 |
別の作業者でも1回レクチャーするだけで、すぐに組立が出来るようになり、技能継承が推進されました。それにより仕事量の平準化もできるようになりました。 |
トルク管理の精度 |
デジタルトルクレンチを使用し、測定値でトルク管理ができるようになりました。デジプロマスタでオーバートルクを許さない設定なので、オーバートルクせず、締付作業ができます。 |
締め忘れの流出 |
設置後、締め忘れのクレームは現時点でゼロです。 |
コスト削減 | トルクレンチの本数削減 15本⇒5本へ 定期的にトルクレンチを更新していたが、デジタルに変え、更新頻度が減りました。 |
工数削減 | チェックシート1台分作成(5~10分)×月22台分=110~220分の工数削減。 他トルクレンチの使用前点検や定期点検の工数も削減。 |
今後について
マスターの内容を誰にでも伝わるようこまめに更新し、熟練の技をメンバーへフィードバックしていきます。
また、作業時間が自動で計測されるので、作業者間の違いを分析することで工数削減に役立てます。